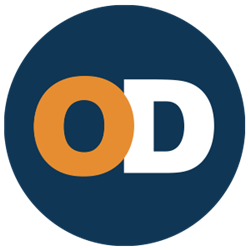
Opendock
“It feels good to know that our software is playing a key role in helping to successfully overcome this pandemic. And being able to get PPE to those who need it most is a critical component.”
SCOTTSDALE, Ariz. (PRWEB)
May 05, 2020
Warehouses and distribution centers that move healthcare-related products are facing serious challenges due to the pandemic. Most were not prepared for the massive surge in volume.
While the difficulty in manufacturing and distribution for household paper products has been problematic, challenges in getting PPE (personal protective equipment) to healthcare workers is a matter of life and death. Indeed, hospital staff and other front-line workers require PPE to properly and safely perform their jobs.
PPE includes medical masks, goggles, clothing, gloves, and other protective gear used by healthcare workers and other first responders. In some cases, getting PPE to those who need it has been a manufacturing problem – the items simply are not available. In other instances, the snag has been with distribution.
Part of the difficulty with distribution during the pandemic has been that warehouses and distribution centers are not well-equipped to handle huge spikes in volume. One reason is that warehouses have a fixed number of dock doors. Even if a given warehouse has additional storage capacity, it can only serve a limited number of trucks at one time. This has created a logjam that has plagued thousands of warehouse facilities as a result of the pandemic.
But a specified number of dock doors is just one of the problems warehouses and DCs are facing.
Because many warehouses have extended their hours to help with the demand, they are being stretched thin on staffing. They are asking more of their existing team members while trying to quickly onboard new staff.
Additionally, the carriers who deliver to and pick up from warehouses are feeling some pain. A large food distributor recently reported lines of trucks of up to two miles and wait times spanning days. Many of the trucks were bringing goods to the warehouse. But a large number of them were waiting to be loaded so they could transport the food products to other DCs or to stores.
While the chaos has been nearly unbearable for many warehouses, others are smoothly handling this throughput challenge by utilizing dock scheduling software, such as Opendock.
Lawrence Dillworth, inbound supervisor at Owens & Minor, noted, “Without Opendock during the COVID-19 volume surge, it would have been a catastrophic failure.” Owens & Minor is a $9 billion manufacturer and distributor of healthcare products.
Opendock allows carriers to book specific appointment times to load or unload freight, solving many of the problems associated with the historical first come, first served model. In that model, trucks compete to get in line as early as possible to minimize their wait time. It’s an inefficient model for both truckers and warehouses.
Opendock CEO, Bob La Loggia, said, “It feels good to know that our software is playing a key role in helping to successfully overcome this pandemic. And being able to get PPE to those who need it most is a critical component.”
Opendock is based in Scottsdale, Arizona. It is a centralized shipping dock scheduling platform that allows carriers and brokers to book appointments with warehouses. With over 25,000 registered users, all major carriers and brokers use the platform daily, including C.H. Robinson, Echo, Schneider, XPO, DHL, and Estes. Additionally, some of the largest shippers in the world also use the system, such as Cargill, Ecolab, International Paper, Pepsi, and others. To learn more about Opendock, click here.
Share article on social media or email: