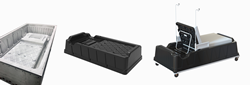
Tooling Tech Group has produced the thermoform tooling for this hospital bed base and backrest.
We are honored that TriEnda put their trust in TTG’s capabilities and happy that we could contribute to a project of such significance. I also commend our employees for producing this tooling within 10 days while still addressing other customer needs.
MACOMB, Mich. (PRWEB)
April 27, 2020
Tooling Tech Group (TTG) announced that it has provided the thermoform toolsets for Emergency & Disaster Relief Beds being manufactured by Kruger Family Industries (KFI) brands TriEnda and Penda. A long-time supplier to KFI, which typically serves the automotive community, TTG manufactured and delivered the bed base and backrest molds within 10 days. This fast response is allowing the two companies to quickly move toward their goal of producing 3,000 beds per day at the Penda facility near Madison, WI, a 300,000 sq. ft. facility, which has been retooled for this project.
“We are honored that TriEnda put their trust in TTG’s capabilities and happy that we could contribute to a project of such current significance,” said Gary Poeppelman, TTG Compression & Thermoforming President. “I also commend our employees for going above and beyond to produce this tooling so quickly, reducing the typical five or six week delivery time to 10 days while still addressing other customer needs.”
The tooling was provided by TTG’s Tooling Technology division located in Ft. Loramie, Ohio that specializes in thermoform, compression, and automation systems. By pulling together its resources and leveraging its vertical integration, the company was able to go from design to finished tool in less than the customer-requested two-week delivery. In addition to the original tool set, TTG has produced three additional bed base tools and two more back rest tools for thermoforming the beds.
These new Emergency & Disaster Relief Beds are lightweight, made of durable 0.350” thermoformed HDPE material, and can be assembled on-site without tools in just a few minutes. A key feature of the bed is their ability to be stacked together efficiently for storage. The nesting allows for a reduction in storage space and quick redeployment in future emergencies.
Deemed a Critical Infrastructure Company, Tooling Tech Group typically partners with the automotive and aerospace industries. Like many companies, it is currently working with several customers who are focused on manufacturing essential products for the medical industry. For more information on its medical related products, visit https://www.toolingtechgroup.com/flexbase/
About Tooling Tech Group
Tooling Tech Group (TTG) builds custom automated systems for assembly, joining and inspection as well as tooling for a variety of applications including thermoform molding, high compression composite molding, blow molding, rotational molding, die casting, and stamping. Industries served include automotive, appliance, lawn and garden, agricultural, aerospace, marine, and off-road vehicle industries, among others.
Originally founded in 1982, the company has grown organically and through acquisitions to become the second largest tooling supplier in the United States. It has more than 1-million combined square feet of manufacturing space, employs approximately 600 people and has a total of 12 locations across four states as well as a sales office in China. TTG takes pride in its promise to deliver on time, every time. Visit http://www.toolingtechgroup.com for more information.
Share article on social media or email: