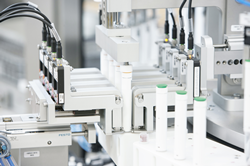
Festo automation at Syntegon
ISLANDIA, N.Y. (PRWEB)
March 30, 2021
Diabetes is on the rise worldwide with around 10 million people being diagnosed with the disease every year, increasing the demand for insulin pens for self-injection. Syntegon’s Danish subsidiary has developed an automated system for assembling these pens using the Festo automation platform.
Flexibility and agility
“By using the Festo automation platform, which includes the servo press kit, we are greatly expanding the flexibility and agility of our systems,” said Michael Andersen, Sales Director of Syntegon Technology in Denmark. “A key component of greater agility is the Festo servo press kit YJKP.”
The YJKP is a preconfigured modular system consisting of software, controllers, and standard electrical drives that can be easily integrated in the plant and offers a high degree of flexibility thanks to the preinstalled software. This means that the modular press system with servo drive for electric pressing and joining up to 17 kN is ready for immediate use and, compared to similar solutions on the market, is both easy to parameterize and cost-effective.
“We have installed more than 100 servo press kits in the automated assembly lines for insulin pens,” said Ulrik Keldke, Head of Syntegon’s engineering department. “The precisely adjustable pressing and joining forces ensure consistent quality and low reject rates. What we particularly like about the Festo servo press kit is that it is quick and easy to commission, and the machine operators don’t need to be trained to use it.”
Quality and safety
“Automating the assembly line is a prerequisite for meeting the requirements for the end product: the insulin pens must be safe and user-friendly,” said Andersen. “The pens must not break when used by the patients, as that would put them at risk. The Servo Press Kit keeps the tension and pressure constant.”
“The glass of the syringes should never be subjected to irregular pressure as they would break,” said Keldke. “The automated systems ensure that the insulin pens are always in order and can deliver the exact amount of insulin.”
Depending on the machine type, Syntegon’s assembly lines produce up to 300 pens per minute. The degree of automation is scalable according to requirements and can also be adapted at a later date. The machine concepts are based either on a rotary table for low to medium outputs or on a linear transport system for high outputs. The system can be expanded with automatic feeders and stations to increase output and the degree of automation.
Consistency and reliability
Syntegon Technology, formerly Bosch Packaging Technology, delivers integrated solutions for its customers. The assembly line for insulin pens can be expanded into a complete line with other systems from the company. Pharmaceutical manufacturers can thus be provided with machines for all process steps, from filling, capping, assembly, testing, to labeling and packaging – preconfigured and from a single source.
The machine control system is based on electrical and pneumatic components and modules from the Festo automation platform. This ensures a consistency of supply since Festo products are available worldwide and offer open interfaces to higher-level controllers. The CPX-E-CEC module from Festo establishes the connection to the process control level, allowing it to be used with Ethernet/IP, Profinet, and EtherCAT. Standardization of components has the benefit of enabling faster time-to-market.
For more information visit http://www.syntegon.com. Go to http://www.festo.us for the full range of Festo products and service offerings. The Festo general information number is 800-993-3786.
###
About Festo
Festo is a leading manufacturer of pneumatic and electromechanical systems, components, and controls for process and industrial automation. For more than 40 years, Festo Corporation has continuously elevated the state of manufacturing with innovations and optimized motion control solutions that deliver higher performing, more profitable automated manufacturing and processing equipment.
Connect with Festo: Facebook, LinkedIn, Twitter and YouTube
Share article on social media or email: