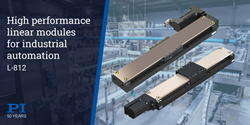
PI’s new high-performance motorized linear modules deliver the precision motion required by industrial automation of advanced processes.
AUBURN, Mass. (PRWEB)
May 07, 2021
PI introduces a new affordable motorized linear module series, L-812, designed for high load capacity and dynamics required by higher load precision motion and automation applications. These high performance linear slides deliver higher throughput in production while watching the bottom line on equipment cost.
XY-Table and XYZ-Table Configurations, Travel Ranges, Easily Configurable
L-812 linear motion modules are available with travel ranges from 102mm to 610mm (4” to 24”) and easily configurable. Two linear modules can be combined to form XY-tables and with the availability of the brake, a vertical axis can be added for XYZ multi-axis motion and precision automation applications. A folded drive train further facilitates integration by reducing the overall length, installing the motor side-by side with the linear stage, instead of the more common inline construction.
The linear modules are designed to allow for easy external relubrication of their low-friction ball screw drive mechanism to provide a longer service life under industrial high duty cycle motion applications.
High Resolution Linear and Rotary Encoder Option, Low Friction, High Load Bearings
The low friction, high-load capacity design with recirculating ball bearing rails, along with powerful motors and high-resolution encoders, enables industrial precision assembly and test automation applications where high tracking performance is critical, and motion errors and settling times need to be kept to a minimum. The linear modules are offered with an option of higher performance linear encoders and lower cost rotary encoders. An absolute measuring encoder option eliminates referencing, saving time and potential errors, sometimes caused when dirt particles cover sections on incremental encoders.
Stepper Motors and Synchronous Servo Motors for Closed-Loop Operation
Synchronous servo motors are preferred in high performance industrial precision motion applications due to their long lifetime, high torque, wide dynamic range (rotational speed range), and capacity to handle overloads. In addition, the low moment of inertia and fast response enable motion with high dynamics and positioning accuracy.
For applications where open-loop control is sufficient and cost is more of an issue, 2-phase, micro-stepped, stepper motors are also available.
Application Fields
Test and inspection, electronics micro-assembly, micro-mechanics and optics assembly and alignment, laser micromachining, materials processing, and medical equipment manufacturing.
Specifications, Datasheet of the L-812 Motorized Linear Modules»
Working with You
PI’s in-house engineered solutions have enabled customers around the world to increase their productivity and technological advantage for 5 decades. With a large basis of proven motion technologies and methodologies, PI is in the position to quickly modify existing designs or provide a fully customized OEM solution to fit the exact requirements of your application from sensors and piezo transducers to microscope nano-focus units, fast photonics alignment systems to multi-axis automation sub-systems.
USA / Canada
http://www.pi-usa.us | info@pi-usa.us | (508) 832-3456
About PI
PI is a privately held company that designs and manufactures world-class precision motion and automation systems including air bearings, hexapods and piezo drives at locations in North America, Europe, and Asia. The company was founded 5 decades ago and today employs more than 1300 people worldwide. PI’s customers are leaders in high-tech industries and research institutes in fields such as photonics, life-sciences, semiconductors, and aerospace.
Share article on social media or email: